How do you set up a custom motorcycle workshop that handles fabrication, electrical, mechanical and everything in between?
We had no idea either, I started in my garage, we moved into our first small motorcycle workshop in Mermaid Beach but quickly outgrew it. Now we’ve had the chance to get a bit of experience and take what we’ve learnt and apply it to a blank canvas.
Setting up what we think is the ultimate custom motorcycle workshop. Sure its still small, but in this set up we’ve used every bit of space we could to ensure we can build high quality machines efficiently (well as efficiently as hand built motorcycles can be). In episode one of our new series – Hard Work, Fast Bikes, Good times, I’ll run you through every bit of clever set up we’ve done in our workshop and office renovation. Sharing with you the ideas we put to use, the tools and benches we’ve made and lay out exactly why we’ve done it that way.
Starting with our Fabrication room, or Fab Lab as it’s been named by Dylan. Enclosing a 4m x 4m space to house our cutting, grinding, welding and sanding. 90% of our dirty work is handled in here, meaning that any of the motorcycles we’re working on outside this space stay perfectly clean. In the room we have our SWS Alumtig 200 welder, a jig table, drop saw, band saw, bench grinder, Oxy torch set up, polisher, linisher, and drill pres. Everything you need to ruin a bike and rebuilt it again.

The Fabrication room is enclosed by a custom steel frame with 1.5 m sliding doors either side, covered with acrylic sheeting. The room is ventilated with industrial exhaust fans installed low on the external wall and ventilation that’s high on the walls, sweeping the air from High entry to low exit. That keeps the air clean and the dust down low.

On the external wall of the fab lab we’ve built and enclosed a materials rack that stores out exhaust tubing, frame tubing, lathe stock, round bar and flat bar. All our materials enclosed and away from grinder dust and moisture to keep it in top shape while in storage.
Outside the fab room we have a ceiling height racking system that stores all of our in progress bike parts, and workshop consumables like hoses, filters, spare batteries and electronics gear, and fibreglass materials. Under this shelving is our Lathe, a consumables and tools locker, our tube benders, a 3-in-1 finger break tool, shop press and eventually our milling machine will be installed here too.

Moving to our motorcycle bay area, we have 2 hydraulic lift tables here with tool boxes and lockers that are equipped for mechanical and electrical work. We do often handle fabrication work out here, but most of the time its lighter, less messy work. Fender brackets, and small frame mods etc. all the heavy lifting like frame builds, exhaust fabrication and sheet metal work is handled in the fish bowl!
In our tin bike bay area we have a few movable tables and a small jig/welding table to wheel around to whatever we’re working on that day. During the motorcycle workshop fit out, I made sure to over invest in storage. Cupboards, and lockers are placed around the shop to make sure during clean up every day, we have a place to store and organise everything neatly.
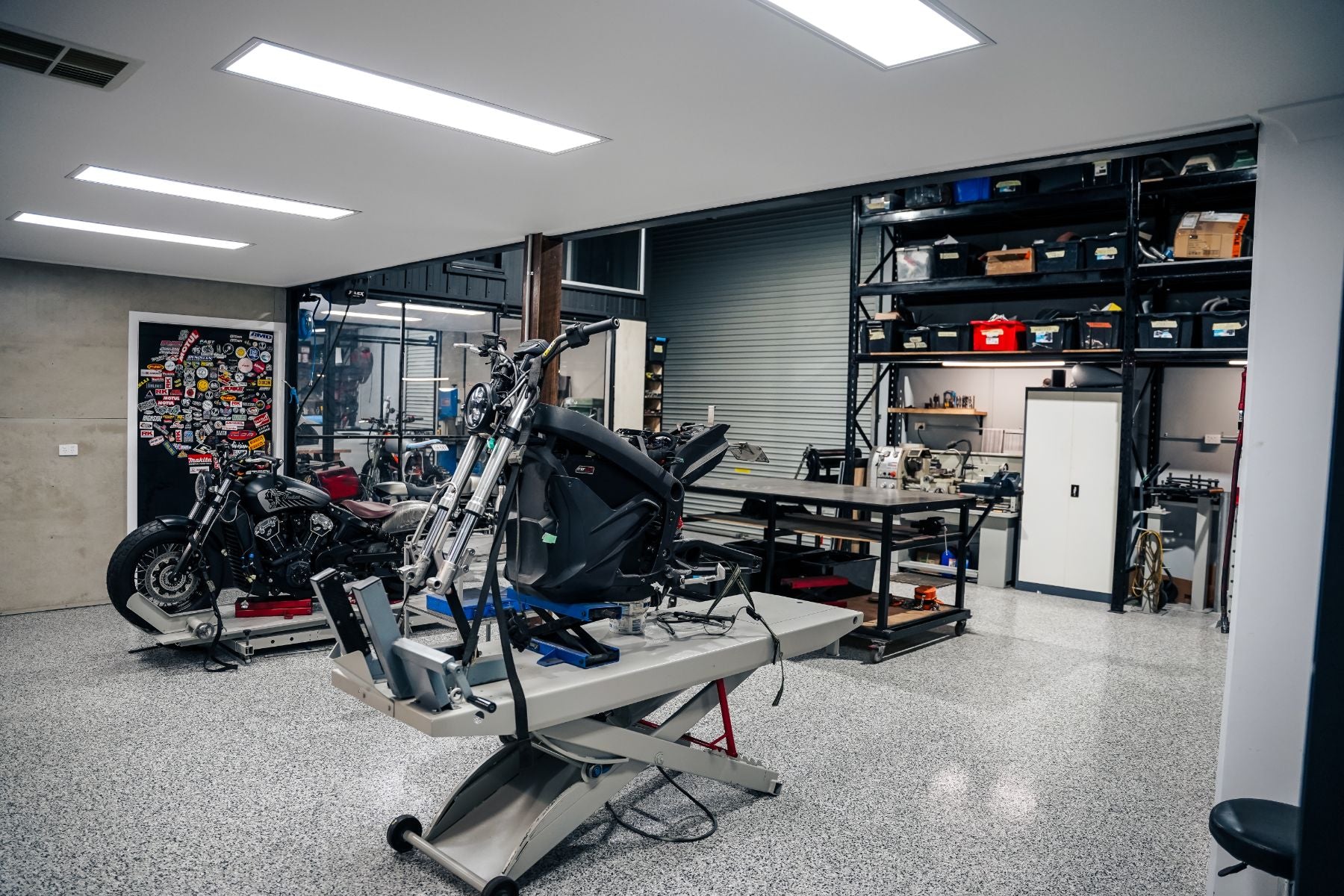
The final piece downstairs was the epoxy flaked floors throughout the workshop. This was high on the priority list. Having the floors sealed is important in terms of cleanliness of the workshop, and the aesthetic of our space. I wanted our clients to come in and be reminded of the Formula one workshops they see from their favourite team. Having a vibrant, well organised and clean space is a really important thing for me to be able to work at my best and create without distraction.
Upstairs on the open mezzanine Dylan and I fabricated up a few motorcycle racks that are up in the roof, with removable benches the bikes can be strapped down and lifted up into the racking to get them off the floor. A great way to save a bit of space of we have projects that aren’t getting worked on for a little while. These sit on either side of a hand built gate emblazoned with the PBM shop logo. Steel construction that’s been water jet cut and backed with white acrylic panelling.

Up the staircase we have a wall of fame with shots of our escapades, adventures and the people we meet along the way. The staircase in the workshop was re-purposed from the old fit out, and sealed in a poly-urethane tub liner used in truck and ute beds. Hard wearing, grippy and will stick to just about anything, it looks pretty good too.
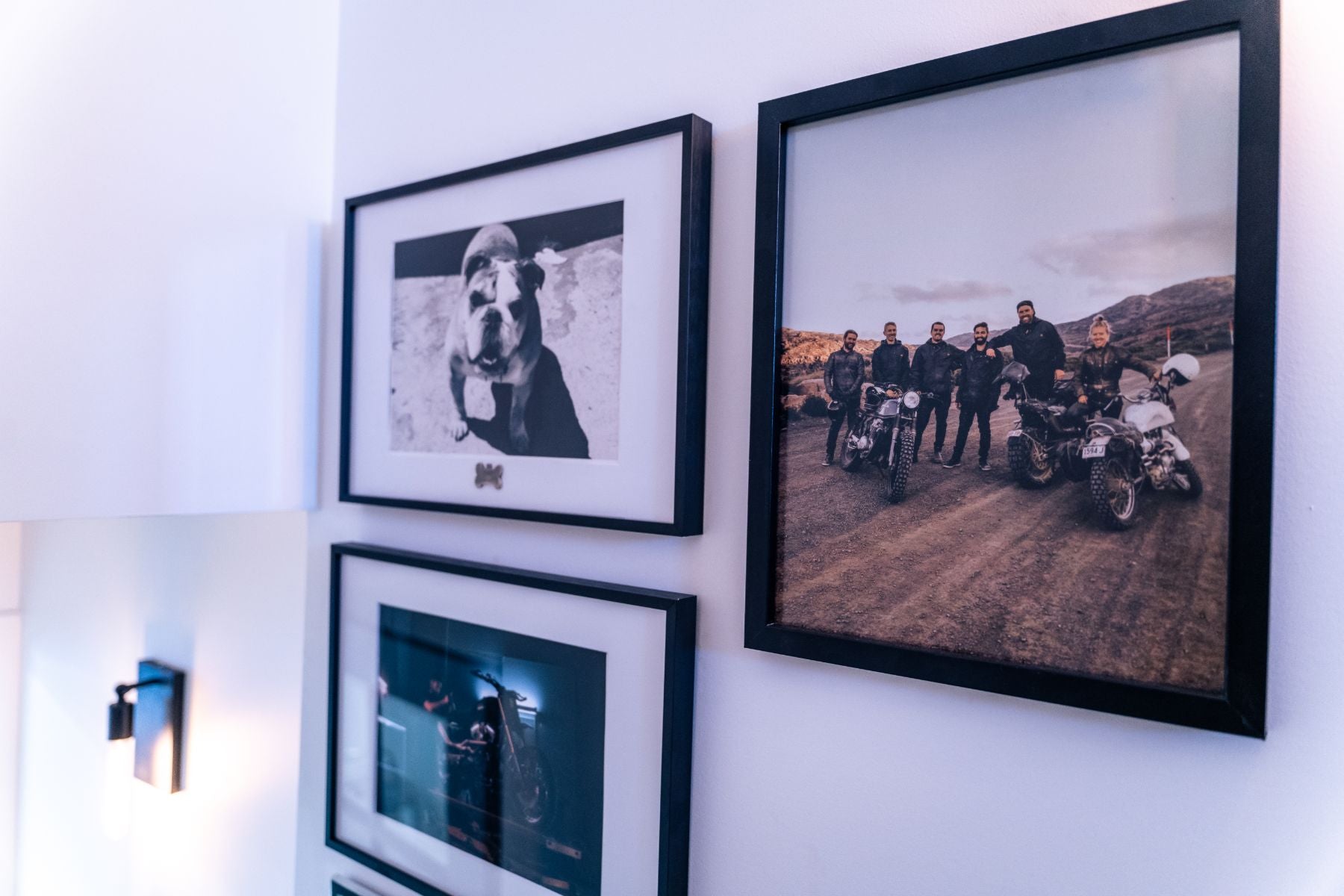
Upstairs I’ve built in a kitchen and lounge area with a separated office that I work out of. A quiet place to design, think and make sure we’re moving in the right direction. Outside of that is our warehousing storage for the E-commerce parts and an order packing area.
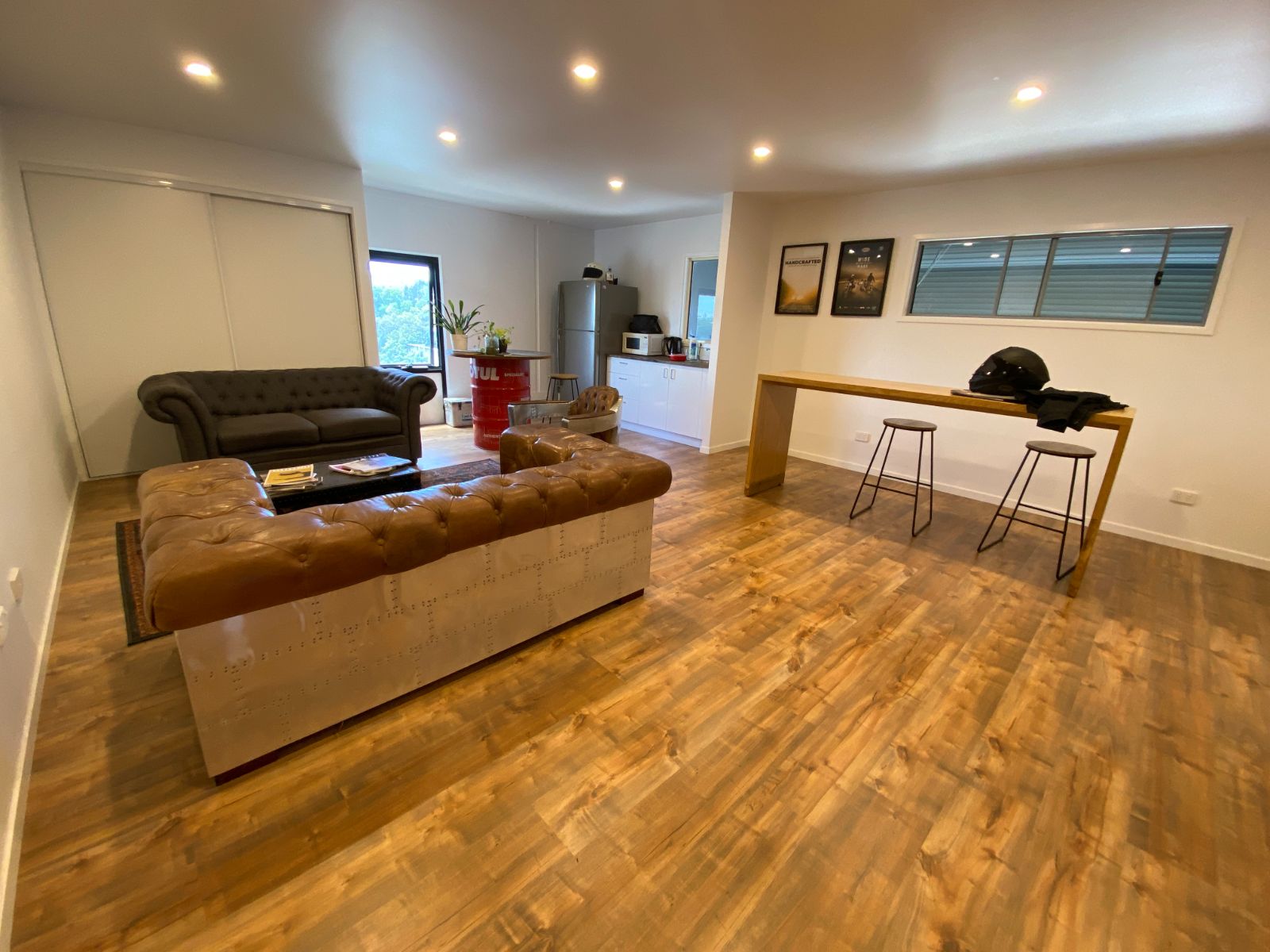
If you have any questions about specific parts of the shop fit out leave me a comment below and I’ll answer it! Episode 2 of our YouTube series we’re going to get busy with our XS650 chopper build, tearing it down, building a hard tail and running a bike reveal with our new neighbours and mates at Burleigh Brewing. Make sure you subscribe to the channel and never miss an episode or bike release!
WE BUILD BIKES WITH PURPOSE.
Purpose Built Moto is home for unique custom motorcycle builds. We offer a unique motorcycle customizing experience in the heart of the Gold Coast.
