We first tried our hands on an Indian Bobber late in 2020. We took quite a departure away from the Bobber style as its usually known sculpting a wild sheet metal tail that to my eye better suited the Indian’s tank. That job has led us here. Our client Jason was introduced to PBM through a friend, what is a pretty unusual way to find yourself a custom bike builder.
Generally our clients find us online, or through our social media channels, follow our work for a while and eventually fall in love enough to pull the trigger on their own hand crafted motorcycle. Jason came in guns blazing and within a few weeks of hearing about us, we had his brand new 2020 Indian Scout Bobber twenty roll through the shop.
The brief was reasonably simple, and left us a lot of room to get creative. The Indian Bobber was to get a custom set of wide wheels, keep it all blacked out, and a completely off the wall exhaust. The idea was to streamline the bobber, beef it up and I wanted to improve the performance on this thing a bit.
The Indian rolls off the factory line with 100+HP, weighing 245kg, and a cornering angle of what feels like 10 degrees. The power is there, but what good is it if you can only use it in a straight line? Our riders other bike is an MV Agusta F3, generally that means the man likes to ride, so I wanted to make sure this tip through corners a little better.
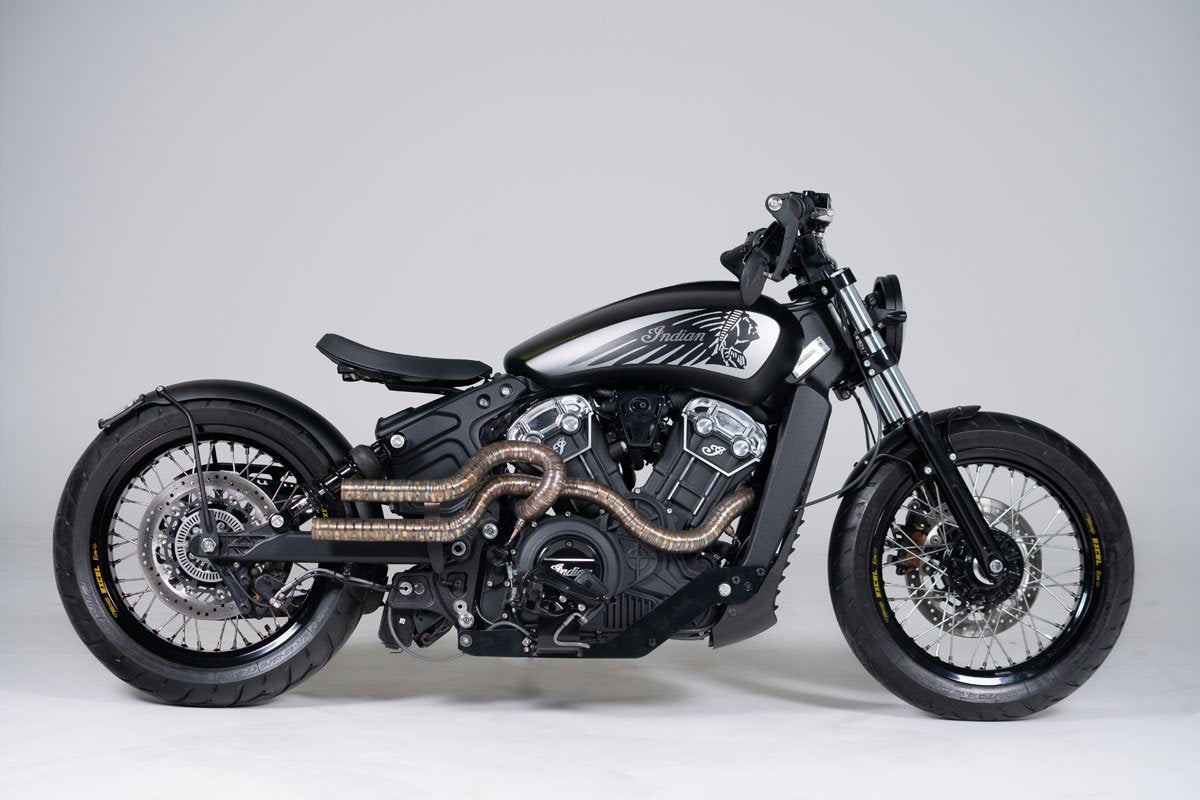
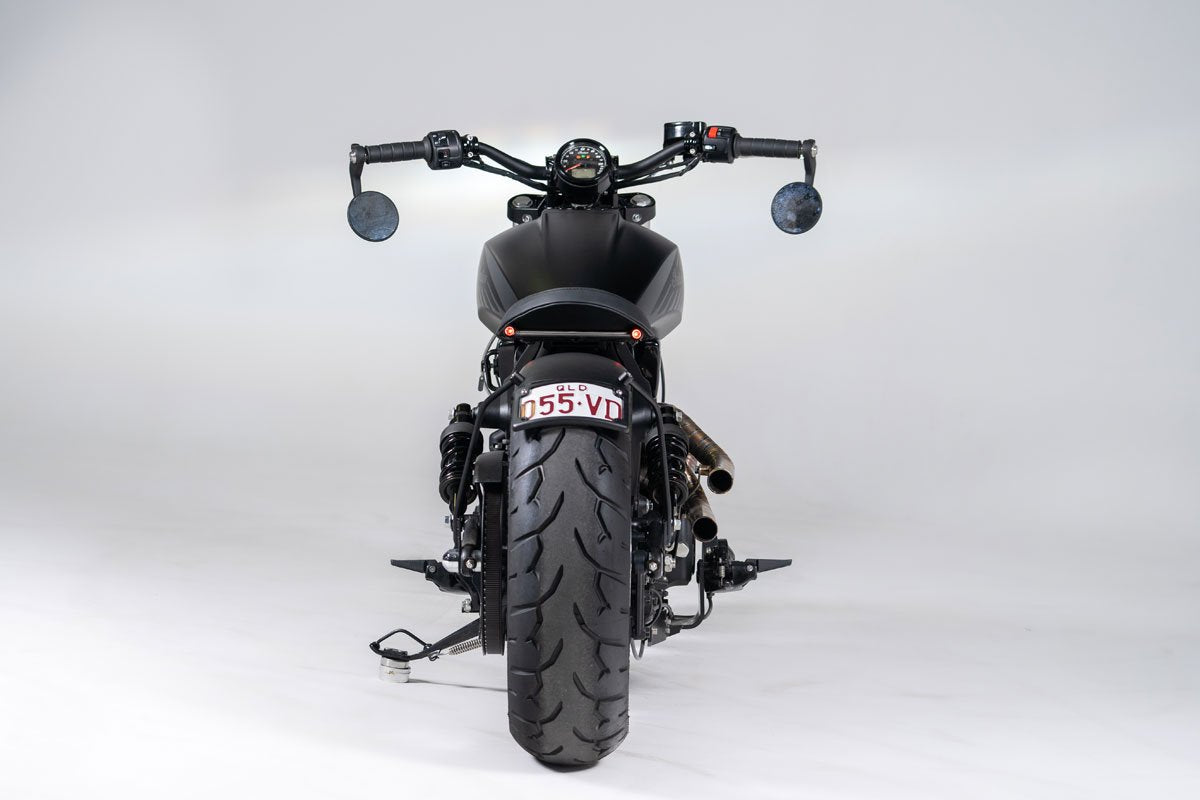
After tear down, our first job was to measure up the wheels, the idea was to run a 200 rear initially, which I figured out you can fit on the Indian with no real trouble. The scarcity of a good quality 18” x 6.00 spoke rim, and a little persuading led us to the decision to use a 180 rear. Setting up the Indian with a 180 x 18 rear, and 130 x 18 front meant the bike would have a better handling set of tyres. The custom Scout sits on a set of Excel Rims, wrapped in Pirelli Night Dragon Tyres.
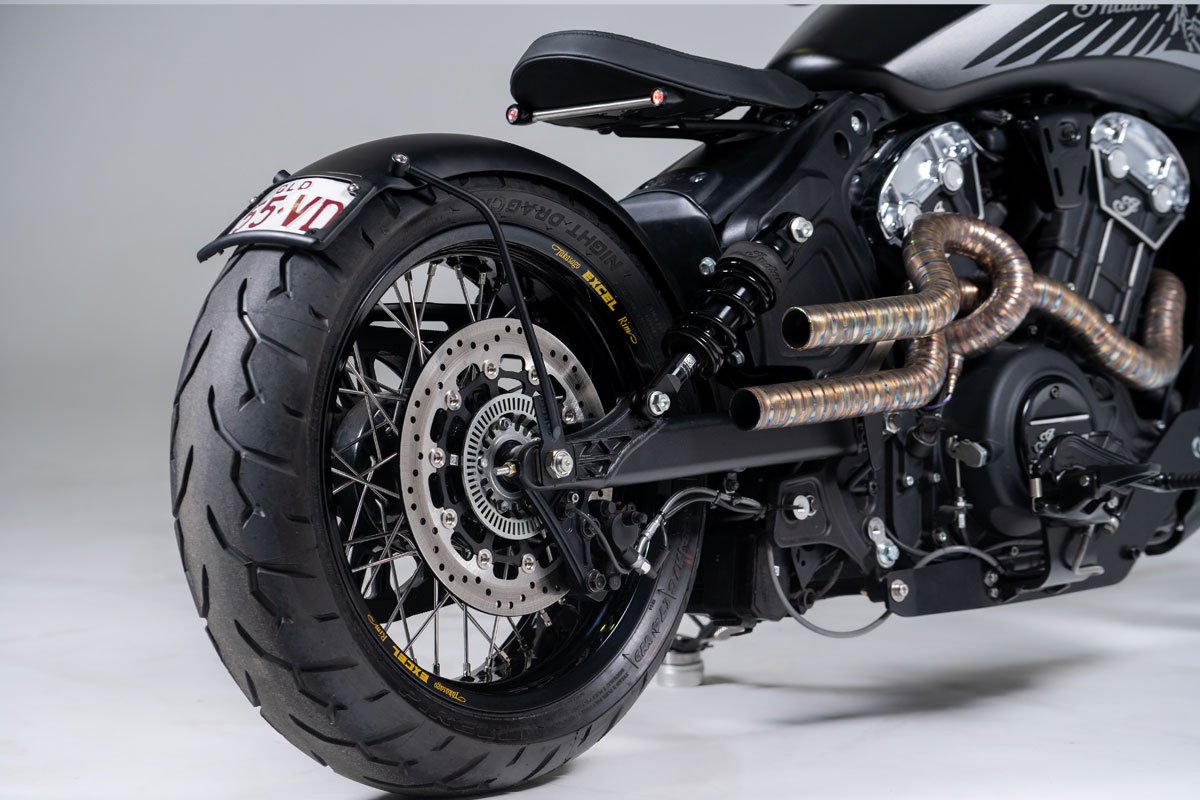
With the wheels on the way, I turned my attention to the bars, and seat mount. We lowered the handlebars considerably with a set of Pro Taper contour bars, and custom risers. That would let me start working on lowering the seat a little too. With the custom fenders to be fitted later, the factory seat mount had the bobber-style seat flying way too high.
I tore down the factory seat, figured out a front pivot mount and chopped the seat pan up. I took 50mm out of the width, and lengthened the seat 80mm with a slightly sharper kick up to better hold the rider in place. The rear seat mount would have to wait until the rear fender was finished.
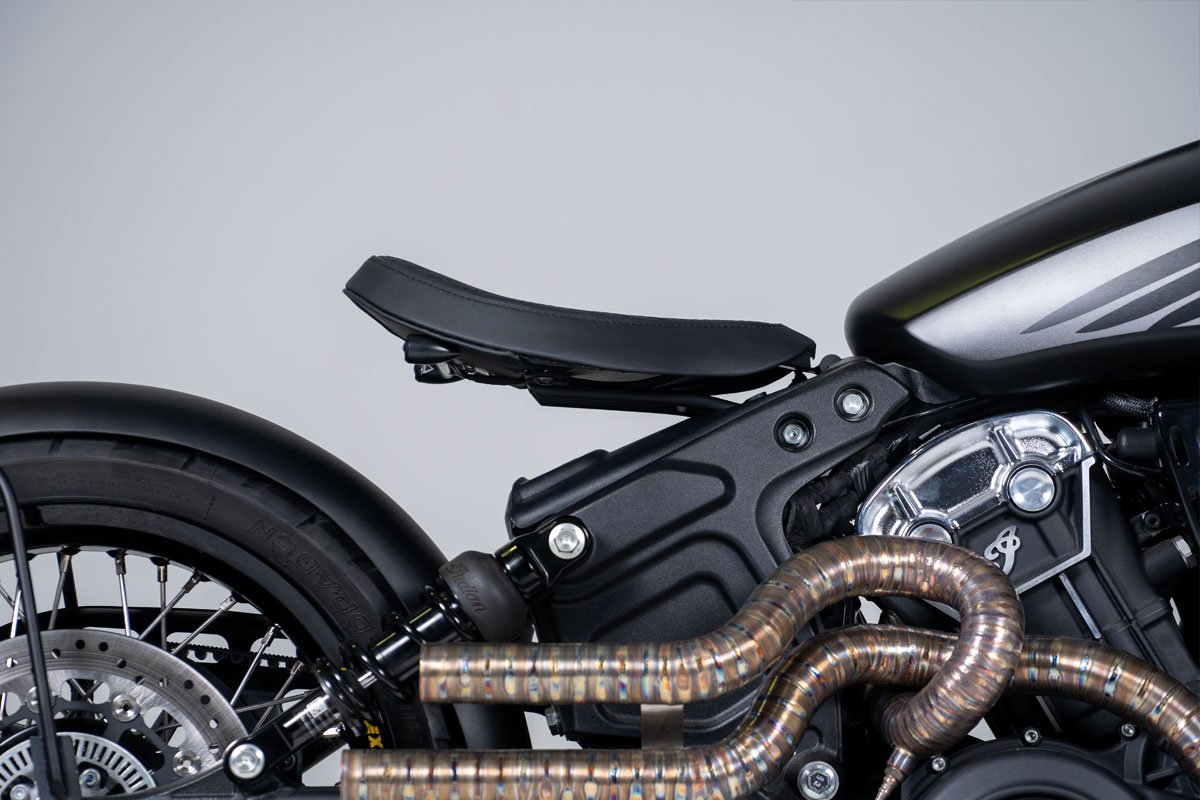
To complete the rider triangle, I had a set of mid mount pegs lined up to be put on. The Bobber comes with a set of wide forward mounted foot controls. With the lowered bars they were just never going to work. There are kits available but none of the suit the Bobber range. So I got one anyway and set to work making it fit.
To fit the mid controls on the Indian bobber all you need is the brackets and bolts from Kuryakyn and a set of scout foot peg brackets. All the other parts are interchangeable with a bit of clever fab work.
Custom lighting on these Indians is no easy feat. With a very complex wiring system that turn convention (and common sense) on its head. The mounting was the easy part. The Indian runs a 7” Flashpoint Headlight up front and a set of 3 in 1 LED turn signals tucked up under the seat on the rear. Clean as a whistle. The hard part is making it all work.
The Indians use a switched ground system (if you want to know what that is look it up), in short it means 90% of aftermarket lighting wont easily work on these bikes without an add on.
I used a polarity inverting relay on each light to achieve correct function, an easy fix, but an annoying one. The end result was worth it though. The clean and super bright lighting looks epic tucked up under that seat.
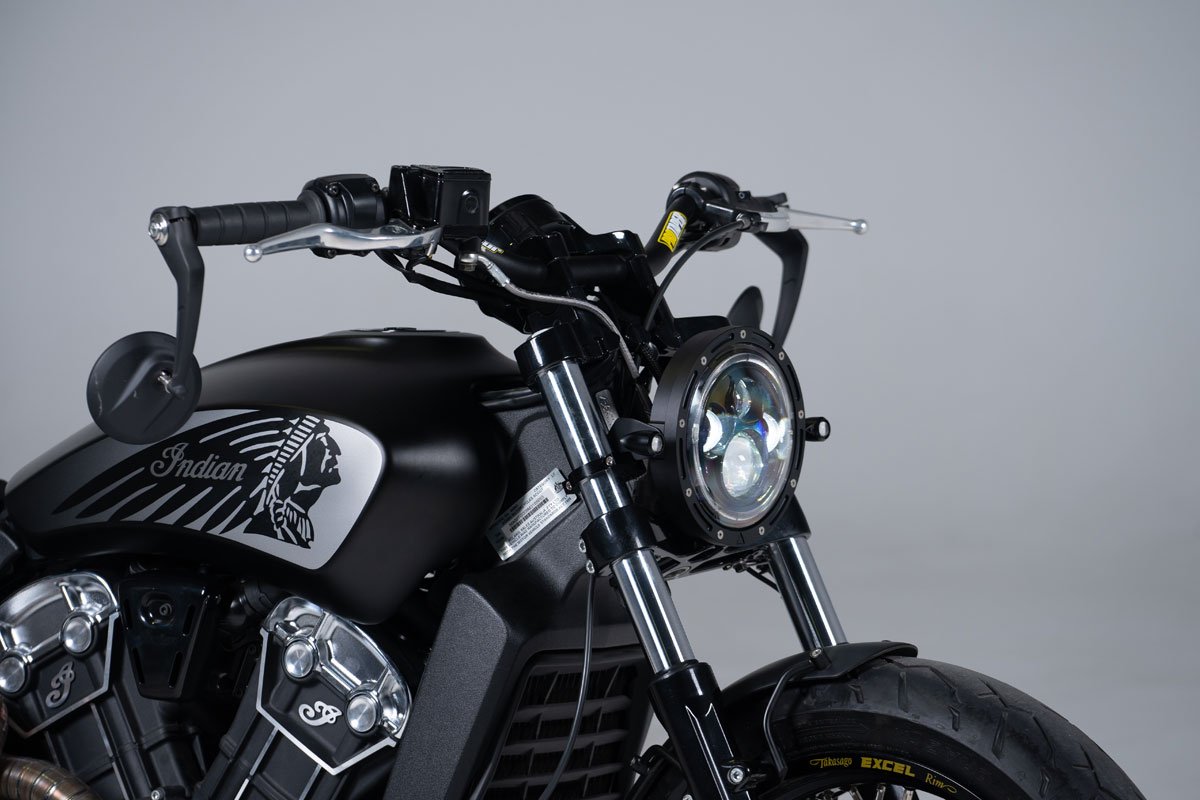
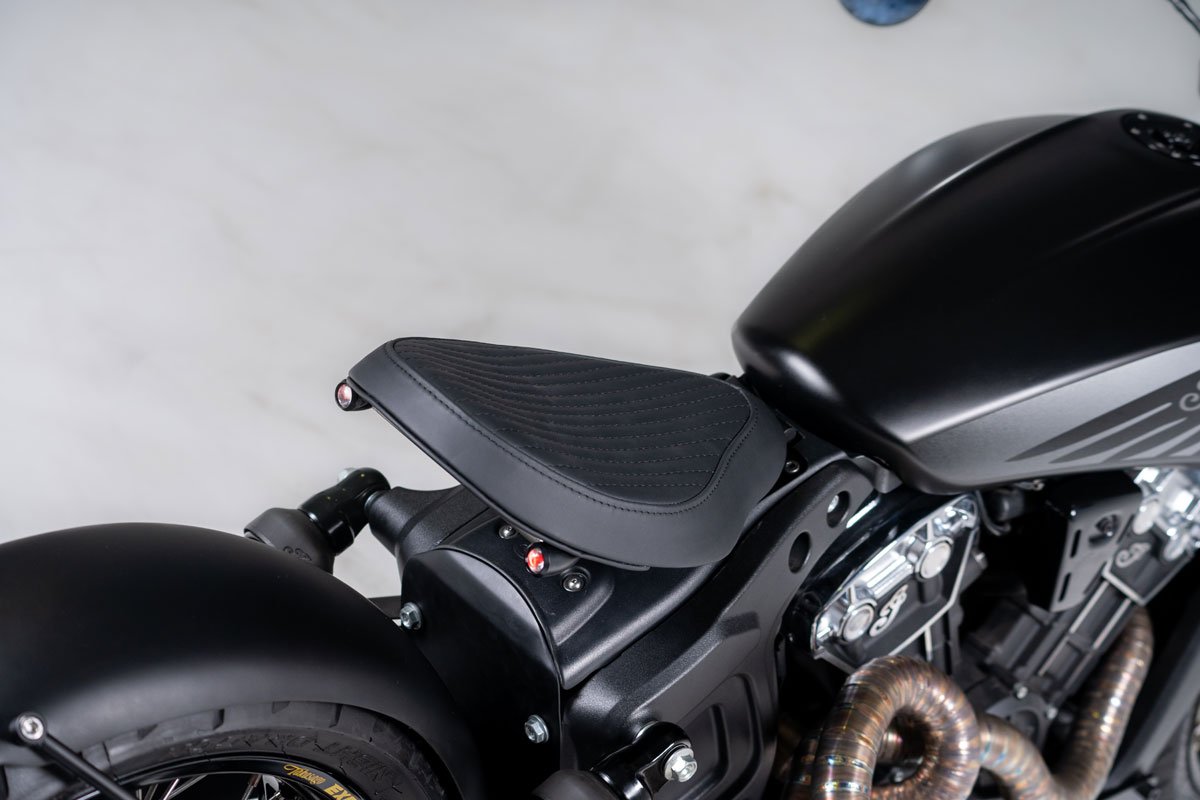
With the world the way it is, the exhaust parts took a while to get to me, but once the 160+ pieces arrived I jumped right in. Jasons request was a complete pie cut system, no matter what it took. I’ve only been building exhausts for a couple years, but the challenge to create something this wild was too enticing.
Piece by piece the exhaust took shape, flowing from the front cylinder, through a swirling rear cylinder header and exiting high down the side of the bike. The exhaust has an integrated pair of mufflers to deaden the rumble just a little, but the bike screams through those pretty well.
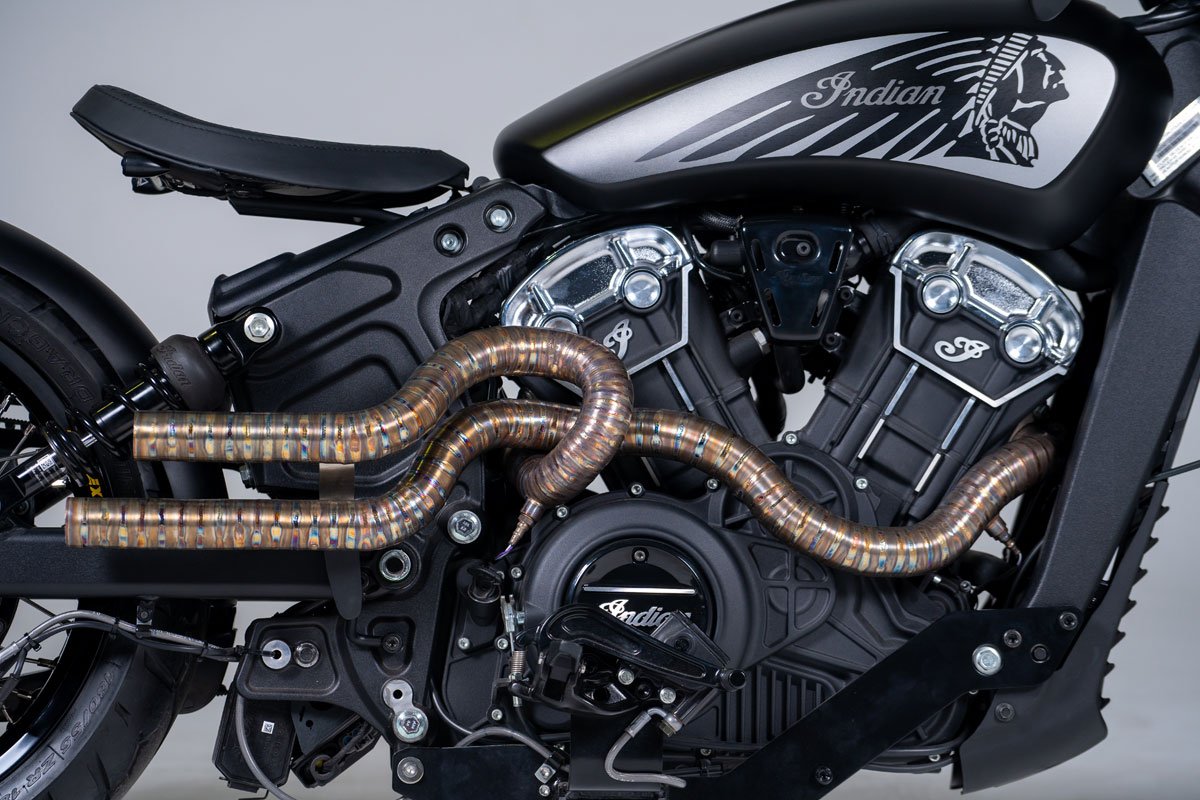
The custom exhaust was to have the heat marks left on, so the entire system had to be meticulously prepared and perfect before final welding. There’s no room for error when you cant just cut it up, grind it back and re-weld something. I was lucky we just picked up our new SWS welder, on the first few welds I had the pulse settings dialled in and it made my life about as easy as it could get when welding 140+ individual pieces together to form an exhaust.
Some quick math on this thing for you fucking nerds out there…
140 pieces @ 45mm Diameter
2πR = 141.37mm
That’s a total of 19.8M of back purged TIG weld.
You can check out the Timelapse video of the Indian Exhaust build at the end of the blog.
All said and done the exhaust system took 4 days to design and fabricate. A day in design and tacking, 2 days in partially welding, adding the required slip joins so it’s easily removed and completing the welding, and a day to build the mufflers and mounts. We burned a lot of time and welding gas on that one, the result speaks for itself. A truly unique piece of work for this custom Indian.
Our last bit of custom fabrication was the fenders and seat mount. With the wide wheels fitted, I trimmed up a the rear fender blank to get fabricating the mounts. Quickly realising it wasn’t radiused correctly. The arch of the fender was too laxed, so I ran it through the English wheel a little, before hitting the spine of the fender with heat to shrink it up to a better radius.
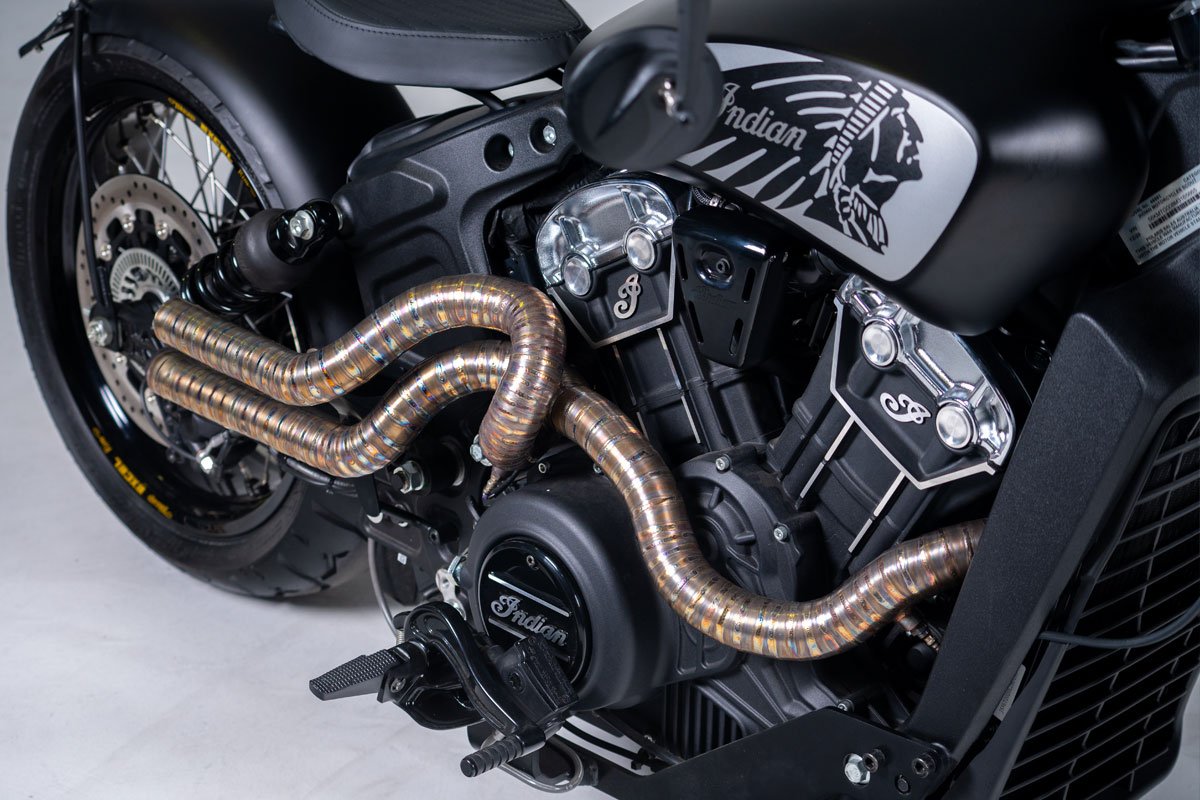
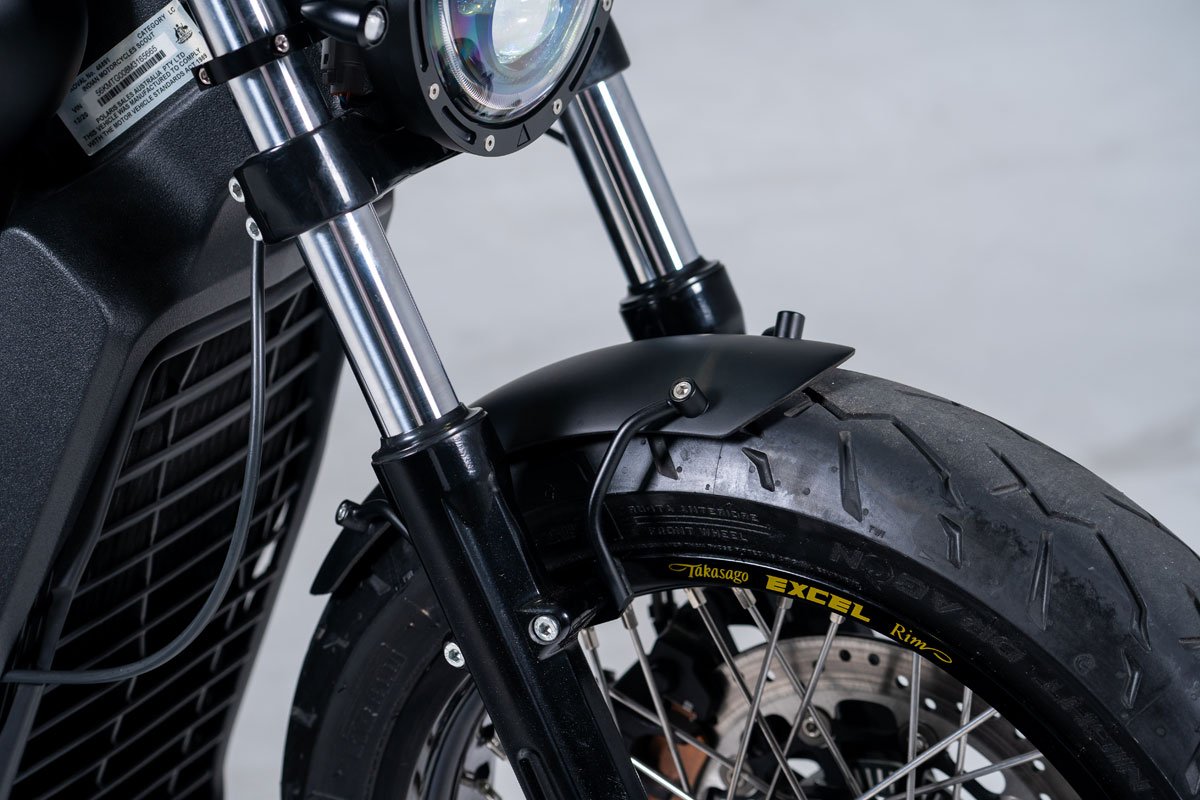
The rear fender would be swing arm mounted to move with the rear wheel. Using some fabrication slugs the front mounts were welded onto the swing arm, and an adjustable plate mount made that hides near the swing arm pivot. The rear mount was fabricated with our M8 fabrication bungs and some round bar, using the rear axle as the mount point. These 2 mounts allow the fender to be adjusted with the belt tension. Making sure as the wheel moves in the adjustment range, you can maintain that perfect fender gap, nice and tight!
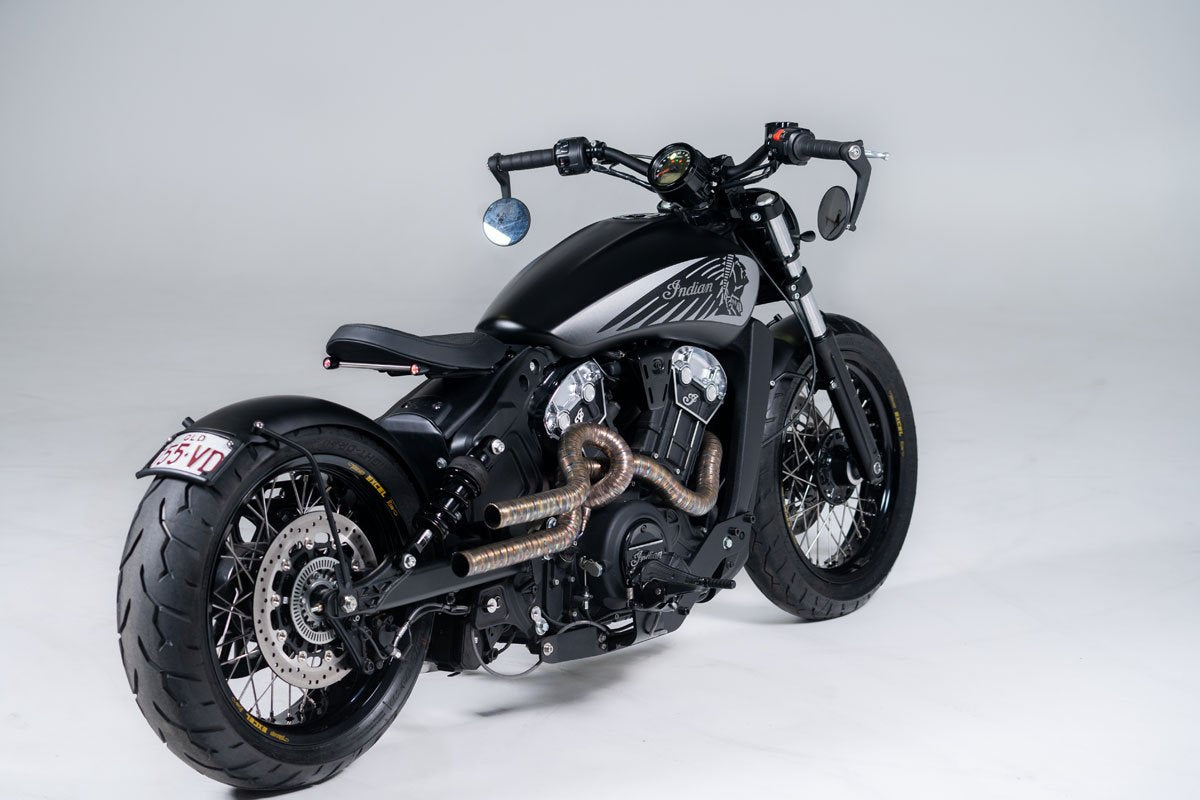
The front fender was built using our PBM DIY front fender kit. A clean Aluminium fender, and the stainless steel bar work you need to mount it up, you can check out a video of how we do it here:
Before the Custom Indian Scout was run up at Dynomite Moto we’ve installed an aftermarket Cold Air intake and Dynojet Power Vision system that will allow the guys to get a perfect tune for the set up we’ve built. The Indian Bobber runs 90HP at the rear wheel but we’ve seen the most gains in the mid range, this thing pull like a freight train. The improvement in the power curve makes fir a vastly more enjoyable ride.
The Custom Indian bobber was finished in a flawless matte black, retaining the factory black/silver tank details. It sits tough on the road, demands your attention and even if you refuse to look, you’re going to hear it anyway. The upgrades on the bobber have it handling like a whole different machine.
Lower bars and mid mount pegs give it a much sportier feel. Leaning through corners and ripping open the throttle lets those wide wheels grip and the performance tune deliver the extra power right to the road. It’s a brute to ride, and you enjoy every minute of it.
Watch the video below to see how we built it and the test ride!
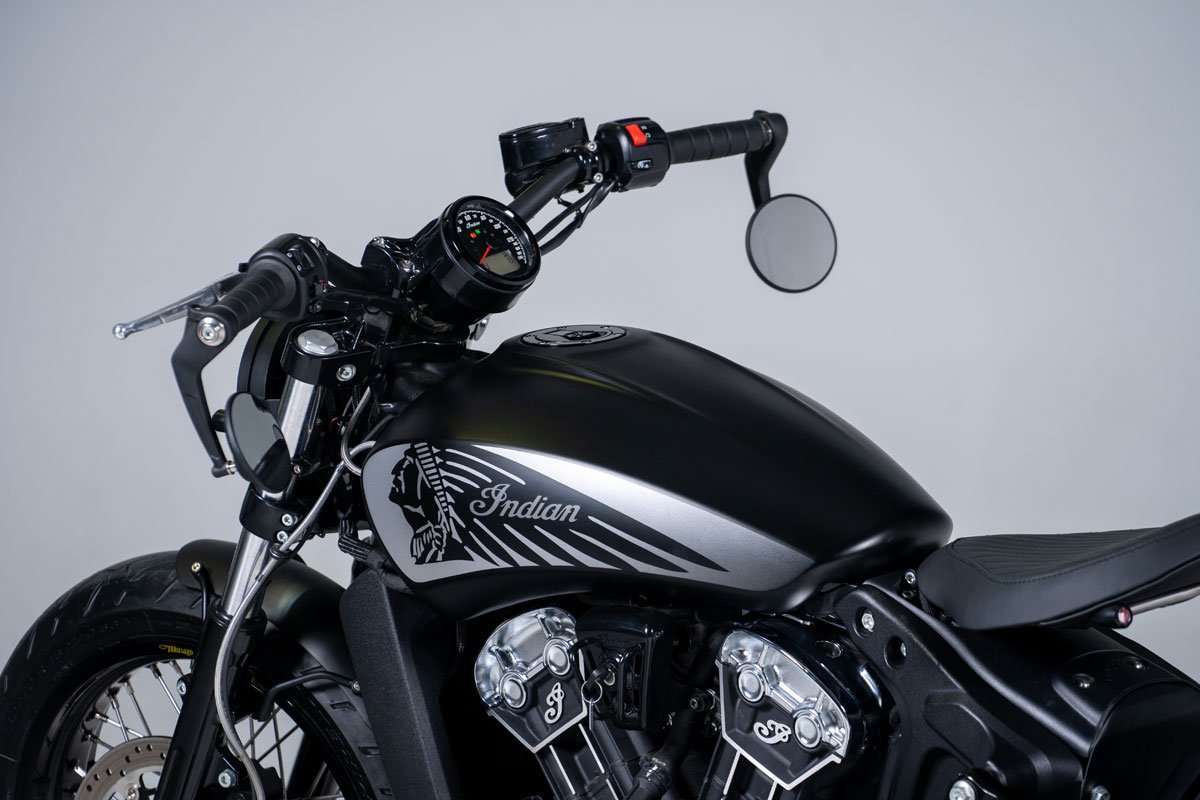
WE BUILD BIKES WITH PURPOSE.
Purpose Built Moto is home for unique custom motorcycle builds. We offer a unique motorcycle customizing experience in the heart of the Gold Coast.

4 reacties
Are these the kurakyn mid controls?
Thanks Morgan, we had a bit of fun with it.
T’ain’t easy bein’ green. I’m heavily envious of your talent, Brother! Fine, fine work!
As Director of QA (and our welding program) for a relatively large construction company, I’ve seen a lot of top hand, fitting and GTAW of stainless pipe and tube. That exhaust system is truly a work of art. Even calling it that seems like an under statement.
Bravo!